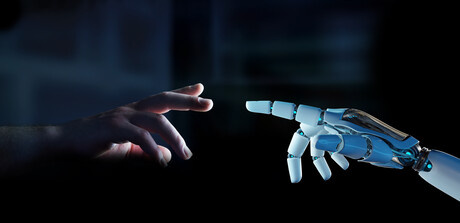
Researchers have developed a soft tactile sensation with skin-like properties.
The team, co-led by the City University of Hong Kong (CityU), applied the sensor to an artificial grip at a real finger and found that it can perform challenging tasks such as sticking hard on sensitive objects and needle thread.
The research gives us a new perspective on tactile sensor design and could contribute to various applications in the field of robotics. The study was recently published in the scientific journal Robotics Science, entitled ‘Magnetic soft skin for high-resolution tactile sensation with force self-separation’.
Imitating the characteristics of human skin
A key feature of human skin is its ability to sense the shear force, meaning the force that causes two objects to slip or slip over each other when they come in contact. By sensing the size, direction and subtle change of shear force, our skin can act as a feedback and allow us to change how we should hold something steady with our hands and fingers or how tight it is. we should get a grip on it.
Researchers Dr Shen Yajing and Dr Pan Jia designed the soft tactile sensor to identify this function.
The sensor is in a complex structure similar to human skin and consists of a flexible film with a special magnetization, about 0.5 mm thin, as the top layer. When an external force is applied to it, it can detect the change of the magnetic field due to the deformation of the film.
Separating
The researchers said that one of the most important features of the sensor is that it can ‘disconnect’.
Disengagement when an external force is automatically disinfected is in two parts – normal force (the force applied directly to the object) and shear force, giving an accurate measurement of those two forces separately.
“It is important to disconnect the outside force because each part of the force has its own influence on the object. And you need to know the true value of each part of the force in order to inspect or control the paperwork or moving condition of the object, ”said Yan Youcan, a PhD student at CityU’s Department of Biomedical Engineering (BME). ) and the first author of the paper.
A robotic gripper with the new sensor completes challenging tasks
By mounting the sensor at the very finger of a robot, the team demonstrated that robots can perform challenging tasks. For example, the artificial fork gripped hard on fragile objects such as an egg while an outside force tried to pull it away, and also threaded a needle with remote control.
“The high resolution of our sensor helps the robotic hand to change the communication position when it grabs an object. And the artificial arm can change the magnitude of the force according to the force’s transmission ability of the tactile sensor, ”said Dr Shen.
Applications
Designing a flexible, intelligent gripper is one of the challenges that has prevented the use of robots for various applications in the food processing industry.
The combination in shape, weight and strength of natural food products has made them difficult to handle for artificial adhesives.
Currently, the CityU soft tactile sensor is still in its infancy and its potential remains unmatched.
But breaking down barriers to what makes an artificial fork different from a human hand may increase the chance that the technology can be used in a variety of applications.